PCB Thickness Guide
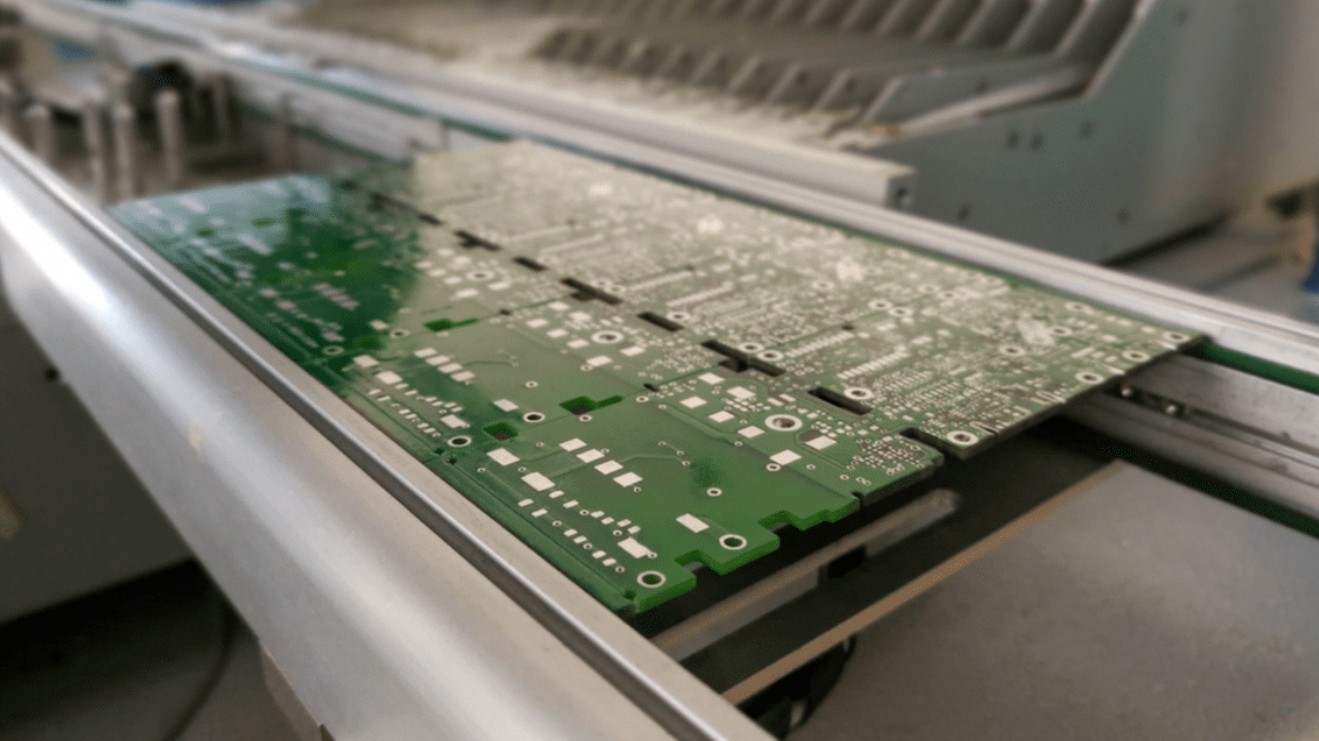
When manufacturing PCBs, Singo regards PCB thickness as a very important factor as it affects the power handling capability of the board.
Thick copper on a circuit board will increase its price, but thick copper is sometimes required. The increase in cost is not only due to the cost of raw materials but also because it takes more time and effort to process thicker copper.
Composition of PCB Thickness
To understand PCB thickness, it is necessary to know what constitutes the thickness of a circuit board and its composition. The PCB thickness specified by the customer is the thickness of the finished board. The nominal thickness of the copper-clad laminate is:

For fiberglass boards, the thickness consists of the respective thicknesses of fiberglass, epoxy, and copper foil. For multilayer boards, the thicknesses of the constituent parts of the individual layers make up the total thickness of the PCB. Among them, the thickness of the copper foil is very important.
PCB Copper Thickness
PCB manufacturers specify copper thickness in ounces. Copper thickness varies according to the type of board they are made of:
- Exterior copper thickness for the regular board - 1 oz. / 1.37 mil / 35 µm
- External copper thickness of switching power board - 2 oz. / 2.74 miles / 70 µm
- Exterior copper thickness for high current power boards - 3 oz. / 4.1 miles / 105 µm
- Internal copper thickness for multilayer boards - 18 µm or 8 µm
In printed circuit boards, 1 oz is used for the main part. The thickness of the copper clad depends on the purpose of the circuit board and the strength of the signal voltage and current, of course. Manufacturers may use 2 oz for parts that handle excessive current. or 3 oz. copper thick. In order to improve the yield rate, PCB manufacturers use the same thickness of copper foil on both sides of the inner layer.
Printed circuit boards with ultra-high-density graphics can use 12μm copper thickness to make thin boards.
Singo recommends using as much space as possible between copper features. This is because it is easier for manufacturers to etch equal-width traces and spaces than thinner spaces between features.
The general rule is to distribute the copper as evenly as possible across the board - not only considering how thick each layer of copper is, but also how far it is spread between layers, as far as possible.
Because etching and plating are organic processes, manufacturers do not have precise control over where the process removes or adds copper. Although the mask protects the intended image from the etchant, the chemical dissolves the copper at different rates depending on where the features are on the board, where the board is in the slot and the density of the copper features on the board.
PCB boards with vastly different copper densities can be problematic as manufacturers agitate and circulate chemical solutions during etching and plating to minimize inconsistencies. Therefore, designers must distribute copper throughout the board instead of creating large open spaces with the ability to isolate copper.
PCB Core Thickness
The core of a PCB, also called a substrate or dielectric, is an insulating material that separates two conductors or layers of copper foil. Therefore, the core is the constant thickness copper-clad material that manufacturers use in the PCB manufacturing process.
For a two-layer PCB, the central substrate will have two copper layers, often referred to as the top and bottom layers.
Substrates are usually manufactured in a standard thickness of 1.6 mm for 2, 4, and 6-layer boards. For more layers in the board, the manufacturer may reduce the thickness.
Characteristic impedance or mechanical reasons may require a thicker substrate of 3.2 mm or a thinner substrate of 0.2 mm from the manufacturer.
Prepreg Thickness
Multilayer printed circuit boards may have two or three prepreg layers. These are fiberglass fabrics filled with resin. The manufacturer places them between two cores and presses them together with the core.
While core materials retain their thickness after pressing, prepregs change their thickness. Therefore, manufacturers can use prepregs to vary the thickness of the PCB. The thickness of a PCB with prepreg depends on its process, as well as the ratio of copper and non-copper areas on layers.
PCB Inner Layer Thickness
In addition to the ordering of layers, manufacturers can also customize the stack up by defining the internal PCB thickness. This is the vertical distance between layers consisting of copper tracks. However, the manufacturer cannot arbitrarily decide the internal thickness.
PCB manufacturers derive the internal thickness based on the specific construction sequence of the board. This means that in order for a printed circuit board to achieve a certain thickness, a manufacturer must employ a certain structure to manufacture it.
PCB Thickness Standard
There are various standards for printed circuit boards, including IPC/JPCA, JIS, JPCA, UL, and more. Depending on the material used by the manufacturer and the standards identified by the PCB, its thickness may vary.
In addition to substrate thickness, copper foil thickness, plating thickness, prepreg thickness, surface finish thickness, and solder mask thickness also have an impact. Also, it depends on the material the manufacturer uses for the board.
Since PCB design software has no built-in provisions to define or control PCB thickness, Singo recommends explaining the required PCB thickness to the manufacturer. Therefore, if the customer wants to control the copper thickness on the PCB, he can write a request for the manufacturer to use a copper-clad laminate with an appropriate copper weight.
The above introduces some relevant information about PCB thickness. If you want to know more or order PCB boards, please contact us.
Singo is a professional custom PCB board manufacturer. The products involve home appliances, digital products, industrial control, medical equipment, etc. After years of hard work, we have established long-term cooperative relationships with some internationally renowned companies. Some of our products are frequently required to operate in harsh environments where quality and reliability are critical. With many years of experience, we have won a good reputation from customers in the field of electronic production with reasonable prices, abundant resources, and on-time delivery.