Common Flex PCB Surface Finishes
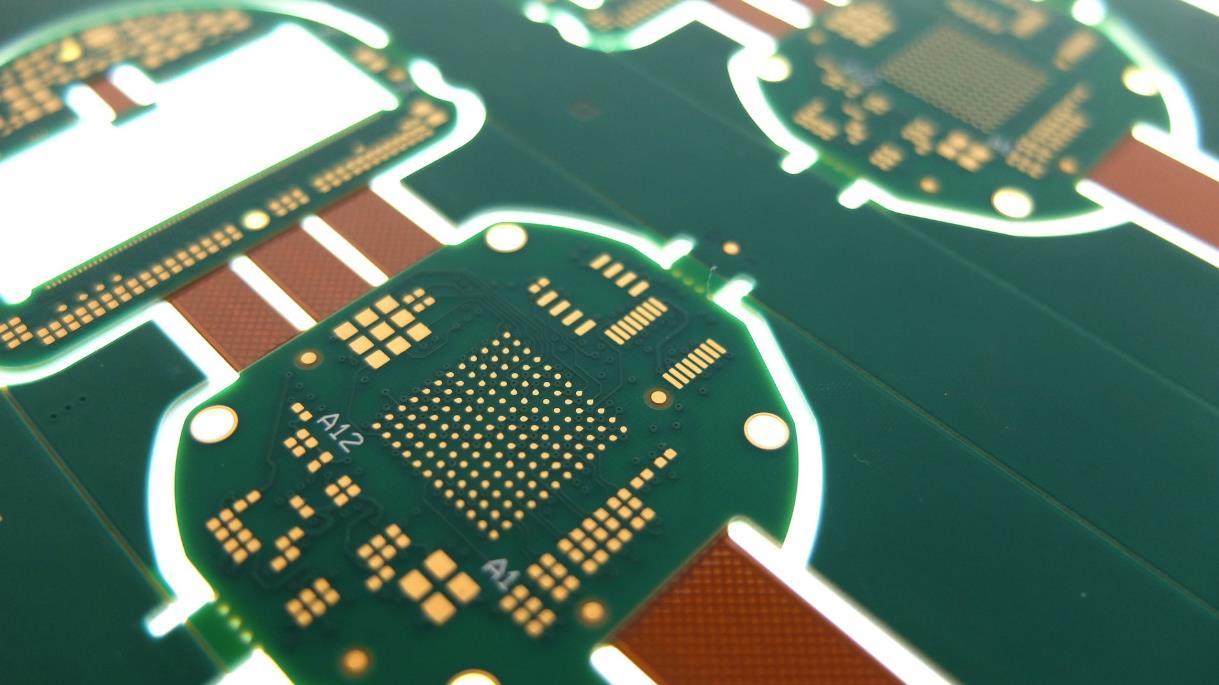
Printed circuit boards, or printed wiring boards, have become an essential part of nearly all areas of modern technology. Copper traces are critical elements on circuit boards. Copper always plays the role of transmitting electrical signals to the different components throughout the circuit board assembly. Without traces, the PCB will not work. Of all the elements that make up a PCB board, copper is one of the most important.
Why choose copper to make PCBs?
The amount of metal used in the PCB is small and thin. One ounce (1oz) of copper can become 35 microns (μm) about 1.4mil thick and can cover a 1ft2 or 0.093m2 PCB substrate. There are many reasons why people in the PCB industry choose copper to make printed circuit boards.
High conductivity
Good flexibility
High-temperature resistance
Good chemical resistance
Easy to obtain
Sufficient supply and fairly low cost
Faster etch rate than many metals
Why is surface treatment required for copper properties?
Copper used in PCB manufacturing has many advantages, but copper also has a specific disadvantage, which is that copper corrodes faster than many other metals. This slough causes oxidation, known as a "back pad," which hinders bonding, welding, and fusing, and creates high electrical resistance in surface contact. Therefore, most flex circuits and rigid boards require a surface finish to cover copper features. There are 4 main considerations for the surface finish of copper features:
1. Prepare for soldering: Soldering assembly is probably the most common operation for flex circuit assembly. Welding is actually a fairly complex process as different metals flow together and combine to form a new alloy, creating an intermetallic layer. This metal-to-metal connection creates an excellent electrical and mechanical bond. Soldering requires a very clean surface and almost any degree of oxidation will hinder the process, so the surface preparation needs to remain copper oxide-free until soldering is complete.
2. Resistance to surface wear: Applications involving surface contact present different challenges. Dome switches and pressure-type connectors make multiple contacts with flex circuits and rely on corrosion-free surfaces for adequate electrical contact. Since mechanical wear can damage soft surfaces, hardness against wear is a key feature.
3. Wire bonding assembly: Wire bonding imposes different requirements on the surface. Ideally, the surface must be free of oxides and soft enough to form around a wire or ball that is pressed against the surface by heat. The metal surface must be compatible with the metals used in wire bonding and be able to maintain good electrical and mechanical connections indefinitely. Both gold ball bonding and aluminum wedge bonding are widely used for direct die-attach components.
4. Bendability and flexibility: Another consideration when choosing a surface finish for a flex PCB is bendability and flexibility. Metals such as tin, gold, and solder may not be able to withstand bending or bending, so a more flexible finish may be required or the finish needs to be selectively applied. Feature density is another factor that eliminates certain surface finishes as a viable option. For fine-pitch components or small vias, surface topography and thickness play a critical role in the successful component assembly.
Typical surface finishes in flexible PCBs
Most flex PCB manufacturers offer a variety of finishes as application requirements vary widely. Below are some typical single-surface finishes in flexible PCBs.
Organic solderability preservatives (OSP)
OSP is the most environmentally friendly (RoHS-compliant) finish and is fairly inexpensive. OSP is applied by spraying or dipping and is usually formulated to bond only with copper. OSP has a limited shelf life, and while it does a reasonable job of inhibiting corrosion, a corrosive flux is often required to achieve excellent soldering results. OSP should be considered short-term to prevent oxidation.
Electroless nickel/immersion gold (ENIG)
ENIG, or Immersion Gold for short, is considered by many to be the ideal RoHS-compliant surface, a RoHS-compliant solder paste reflow finish. The surface is not only receptive to solder but also very smooth and flat, making it easy to place small components. ENIG is also an acceptable surface finish for direct die attach using aluminum wire bonds. Electroless nickel is used as a barrier metal between gold and copper to prevent copper from migrating into gold and avoid corrosion caused by the action of electric current. Immersion gold is thin enough (typically Au: 2-3μ'', Ni: 120-240μ''), so there is no gold embrittlement problem.
Immersion silver
Immersion silver processing is most often used when the solder paste contains silver to enhance compatibility with subsequent soldering processes. Silver dissolves into the solder during reflow. While storage conditions can affect shelf life, Immersion Silver is considered a RoHS-compliant surface with a limited shelf life. It should be soldered shortly after fabrication. Silver should not be left on copper indefinitely because it is prone to dendrite growth.
Silver also has a tendency to oxidize, but this is usually more of a cosmetic issue than a surface contact issue, as silver oxide is actually very conducive.
Immersion tin
Immersion tin, also a RoHS-compliant surface, behaves like immersion silver. It has a coating thickness of about 25-60μ'', which provides excellent protection against short-term oxidation. Over time, the tines can oxidize and dendritic growth problems can also occur. The immersion of tin in copper forms an intermetallic layer. Over time, the copper-tin intermetallic layer continues to grow. Flexible PCB soldering must be done on the tin, not directly on intermetallic alloys. If it takes too long, there won't be enough in for adequate soldering.
Hard gold
Applications requiring highly conductive surface contacts present different challenges. Hard gold is typically a flexible PCB finish with tactile metal domes, molded rubber domes, and pressure-type connectors. These copper properties rely on corrosion-free surfaces to achieve low-resistance electrical contacts. In these cases, the surface finish needs to be wear-resistant through multiple insertions and/or contacts in common.
Electrolytic hard gold surfaces are solderable, but hardened gold additives can make the process more difficult. The flexibility of this plated surface can also be an issue. While gold itself is very flexible, the nickel barrier metal is somewhat brittle. Hard gold over nickel can generally be used for limited flexings, such as flex mounts, but is not recommended for areas that are often flexed or curved in shape.
Soft gold
Soft gold is typically used for gold ball wire bonding for direct die-attach component assembly processing. Soft gold does provide a solderable surface, but this is an expensive option if wire bonding is not required. Electroless Nickel Immersion Gold (ENIG) will be a more suitable choice when standard surface mount soldering is required.
Like most metal finishes, soft gold/nickel is a RoHS-compliant finish and must be kept away from areas that need to be bent or bent.
How to find the right flexible PCB manufacturer?
When choosing a flexible PCB manufacturer, consider the following basic factors:
Speed of response: If a flexible PCB company's salesperson or engineer can respond quickly to your RFQ or question, it indicates that the company has a good understanding of PCB manufacturing, stacking, and pricing. Like rigid boards, the price of flexible PCBs is calculated in square meters. But before quoting, whether you prefer unit (single) delivery or kit delivery, the boards need to be assembled and stacked. The most commonly used FCCL has a width of 250mm. If your flex PCB is large, we may need to use FCCL with a width of 500mm.
Flexible PCB manufacturing experience: Successful flexible PCB manufacturing requires high-end equipment and extensive experience to guarantee high-quality output. During the manufacturing process, the movement of the flexible PCB material between layers and the thermal expansion and cold contraction of the material is critical to the lamination results and registration. If your circuit requires PCB assembly. Just find and choose a reliable turnkey manufacturer with extensive experience in flex and rigid-flex circuits to ensure they have the capabilities and knowledge needed to meet your project requirements and standards.
Impedance control (if required): Impedance-controlled flex and rigid-flex PCBs are more demanding for modeling and manufacturing. Different materials (FCCL, adhesive, overlay, CCL, and PP) from different manufacturers are different. The provided dielectric constant (DK) values can be inaccurate, online free modeling software often returns incorrect values, and can only model simple trace-to-planar structures.
The above details the common FLEX PCB surface treatments, as well as suggestions for finding a suitable flexible PCB manufacturer, if you are looking for a flexible PCB manufacturer, welcome to contact us.
Singo is a professional custom PCB board manufacturer. The products involve home appliances, digital products, industrial control, medical equipment, etc. After years of hard work, our manufacturing facilities include dust-free workshops and advanced high-speed SMT lines (Yamaha), fully automatic printing presses, lead-free wave soldering, and fully automatic assembly lines. Our die attaches accuracy can reach ±0.03mm on IC parts. This means we can handle almost all types of ICs such as SO, SOP, SOJ, TSOP, TSSOP, QFP, GA and U-BGA.