The Role and Selection Principle of PCB Surface Coating
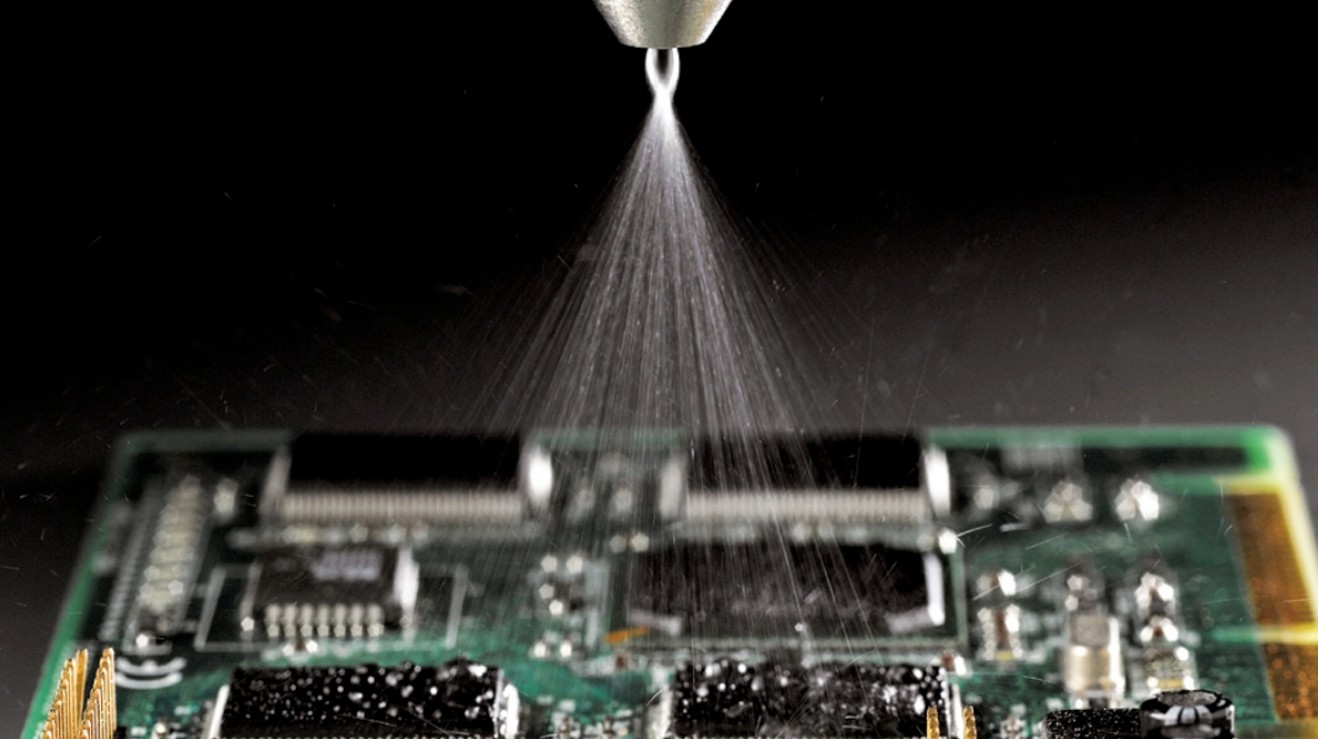
Copper is selected as a conductive material by PCB because of its excellent electrical conductivity and physical properties. However, copper surfaces are easily oxidized when exposed to air, forming a solid but thin oxide layer on the surface, which often leads to defective solder joints, reducing product reliability and shelf life. Therefore, it is necessary to take protective measures to prevent the copper surface from being oxidized, which is the original reason for the emergence of heat-resistant solderable surface coatings. Today, PCB surface coatings are developing rapidly and there are many classifications. How to choose the appropriate type is still a problem. Therefore, this article will discuss the PCB surface coating function,
What is PCB Surface Coating?
Significance of PCB Surface Coating
In order to prevent the copper surface of the PCB pad from being oxidized and polluted before it can be soldered, it is of great significance to perform surface plating (also called surface treatment) on the copper to play a protective role.
Copper has the second-best electrical conductivity and physical properties (best to silver) plus its abundant storage and low cost, so copper is chosen as the conductive material for PCBs. However, as an active metal, copper is easily oxidized, and an oxide layer (copper oxide or cuprous oxide) is easily formed on the surface, resulting in solder joint defects, thereby reducing product reliability and shelf life.
According to statistics, 70% of the defects of PCB boards come from solder joints, for the following two reasons:
Cause #1: Contamination and oxidation on the pads on the PCB often result in incomplete soldering and cold solder joints.
Reason #2: Diffusion between silver and copper tends to create a diffusion layer, while intermetallic compounds (IMC) tend to form between tin and copper, resulting in a loose and brittle interface.
Therefore, the copper surface to be soldered should be implemented with a protective layer with solderability or isolation function to reduce or avoid defects.
PCB Surface Coating Requirements
The surface coating of PCB pads should meet the following requirements:
a. Heat Resistance
At high temperatures during soldering, the surface finish should also be able to prevent oxidation of the PCB pad surface and allow direct solder-to-copper contact.
The heat resistance of organic surface coatings refers to the properties of melting point and thermal decomposition temperature. The melting point of the surface coating should be close to or lower than tin, while its thermal decomposition temperature should be much higher than the melting point of the solder and soldering temperature. Therefore, no oxidation of the copper surface occurs during the soldering process.
b. Coverability
Basically, the PCB surface finish is able to completely cover the copper pad surface before and during soldering without being oxidized or contaminated. Will not drift, disintegrate, or float on solder joint surfaces. Therefore, in order to ensure that the molten solder can be completely soldered to the pad, the surface tension of the molten surface coating should be small and the decomposition temperature should be high to ensure high coverage before and during soldering.
c. The Remains
The residue here refers to the residue left on the surface of the pad or solder joint after the soldering is completed. In general, residues are harmful and should be eliminated, which is why cleaning measures are usually carried out after welding.
d. Corrosive
Corrosion here refers to the corrosion of the surface of the circuit board caused by the residual solder after soldering of the PCB substrate material or metal layer.
e. Environmental Issues
Nowadays, environmental issues are attracting more and more attention from the industry. For the surface coating of PCB, the wastewater during coating generation and after cleaning and soldering should be easy to handle and environmentally friendly.
How Are PCB Surface Coatings Classified?
Based on Manufacturing Technology
According to the manufacturing process, PCB surface treatment can be divided into surface coating and metal coating.
a. Surface Coating
Surface plating refers to the process of adding a thin layer of heat-resistant and solderable coating on the copper surface by physical means. The main performance of the surface coating is that it can provide the solder with a pure copper surface for soldering during the soldering process. Surface treatments, such as HASL (Hot Air Solderability Level) or OSP (Organic Solderability Preservative), fall into this category.
b. Metal Coating
Metal plating refers to the process of generating a heat-resistant solderable metal plating on the pure copper surface of the PCB pad by means of electroless plating and electroplating.
Based on the Application Effect
According to the application effect, the surface treatment can be divided into three categories: flux soldering on the barrier coating, flux soldering on the metal coating of the diffusion layer, and flux soldering on the metal coating barrier.
Category #1: Flux Soldering to the Coating of the Barrier Layer.
The main performance of this surface coating is that the molten solder will float on the solder surface after leaving the copper during high-temperature soldering. However, IMC will be generated at the solder joint interface, increasing the possibility of defects.
Category #2: Flux Soldering to a Metal Coating on a Diffusion Layer.
The emergence of such technologies aims to eliminate IMC, but its shortcomings are also obvious. On the one hand, it tends to cause diffusion; on the other hand, it tends to cause embrittlement of the board, which in turn leads to defects in the circuit.
Category #3: Flux Soldering on a Metal-Coated Barrier.
The main advantage of this technique is that the solder is soldered to the isolated surface of the metal plating, rather than directly to the copper surface. Therefore, no stable IMC will be generated at the interface and no diffusion between metals will occur.
How to Choose PCB Surface Coating?
High priority must be given to PCB surface finish as it is closely related to PCB solderability, reliability, and shelf life. It should be selected according to the application conditions and fields.
Due to the different performance and application effects of the surface coating, it should be selected according to the application requirements and specific application fields in the PCB manufacturing process, and the manufacturing complexity and cost should not be used as the main basis for judgment.
Generally speaking, for electronic products serving the civil industry or general industry, surface coatings such as HASL and OSP should be selected for flux-free soldering.
For medical, transportation, military, aerospace, and other applications that require high reliability and long life, you should choose a surface coating whose flux is soldered to the isolation layer.
The above has introduced the function and selection principles of PCB surface coating. If you want to know more or want to order PCB boards, please contact us.
Singo is a professional custom PCB board manufacturer. Our company is mainly engaged in PCB assembly and OEM/ODM electronic manufacturing services. Products involved in home appliances, digital products, industrial control, medical equipment and so on. After years of hard work, we have established long-term cooperative relationships with some internationally renowned companies. Some of our products are frequently required to operate in harsh environments where quality and reliability are critical. With many years of experience, we have won a good reputation from customers in the field of electronic production with reasonable prices, abundant resources, and punctual delivery.