Types of PCB Assembly Processes
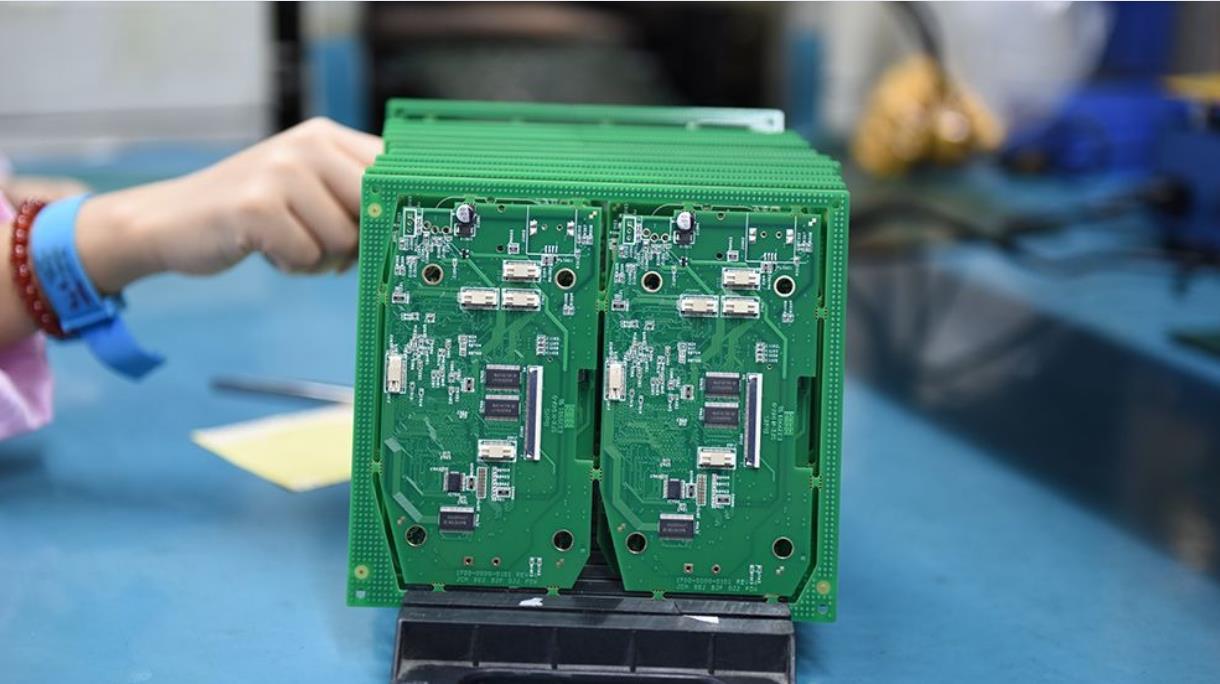
The manufacturing process of assembling a PCB is called the PCB assembly process or PCBA. During this process, the required electronic components are mounted on the PCB.
Copper wires (called traces) on the bare board electrically connect the connectors and components to each other.
These traces run signals between these functions, enabling the board to behave in a specially designed way.
The PCB assembly process consists of several automated and manual steps. For every step of the process, board manufacturers have manual and automatic options to choose from.
In this article, we will discuss three basic techniques of the PCB assembly process.
Through-hole technology (THT) assembly process
Through-hole technology (THT) is a method of building electronic circuits in which pin-through-hole (PTH) components are drilled into a printed circuit board (PCB).
The ends or leads are then secured to the opposite pads with molten metal solder using wave or reflow equipment. This process is also known as a through-hole assembly.
Through-hole technology replaced earlier electronic assembly techniques such as point-to-point construction. From the second generation of computers in the 1950s to the popularity of surface mount technology in the late 1980s, every component on a typical PCB was a through-hole component.
The three key steps of the through-hole technology (THT) assembly process are as follows:
Step 1: Component placement
This step is done manually by professional engineering staff. Engineers need to quickly and accurately place components in the appropriate positions based on the customer's PCB design files.
The component placement must comply with the regulations and operating standards of the through-hole mounting process to ensure a high-quality end product.
Step 2: Inspection and correction
After component placement is complete, the board is placed in a matching shipping frame, where the board into which the component is inserted is automatically checked for accurate component placement.
If problems with component placement are observed, it is also easy to correct them immediately. After all, this happens before soldering in the PCBA process.
Step 3: Wave soldering
The THT assembly should now be accurately soldered to the board. In a wave soldering system, the board is moved slowly over a wave of liquid solder at high temperatures of about 500℉.
Surface Mount technology (SMT) assembly process
Surface mount technology (SMT) is a method of building electronic circuits in which components are mounted directly on the surface of a printed circuit board (PCB) using solder paste.
Electronic devices manufactured in this way are called surface mount devices (SMDs).
SMT components are typically smaller than their through-hole counterparts because it either has smaller leads or no leads at all.
The three key steps in surface mount technology are pasting, placement and reflow.
Step 1: Solder paste printing
Solder paste is applied to the board by a solder paste printer.
A stencil or stencil or solder screen ensures that the solder paste can stay exactly where the components will be mounted.
Step 2: Component installation
After coming out of the solder paste printer, the PCB will be automatically sent to the placement machine, and the components or ICs will be mounted on the corresponding pads due to the tension of the solder paste.
Components are mounted on the PCB via a component reel in the machine. The component spool carrying the component rotates to feed the machine with the part, which will quickly stick the part to the board.
Step 3: Reflow soldering
After each component is placed, the board goes through a 23-foot oven (reflow oven) at 500℉.
The solder paste must be heated until it melts and forms a strong and reliable joint between the component and the board surface. This is achieved by using a reflow oven that heats the solder to the proper temperature and then cools it down to a solid again.
In this way, the SMD components are firmly bonded to the circuit board.
Surface mount devices are typically small and lightweight.
Compared with the through-hole mounting process, the surface mount process is highly automated, reducing labor costs and increasing productivity. SMDs can be one-quarter to one-tenth the size and weight and one-half to one-quarter the cost of equivalent through-hole parts.
Industries that use SMDs include telecommunications, aerospace, consumer electronics, wireless, automotive, and instrumentation.
While through-hole mounting provides a stronger mechanical bond than surface mount technology, the additional drilling required makes the board more expensive to produce. It also limits the available routing area for signal traces on multi-layer boards, because the holes have to go through all layers to the other side. For these reasons, through-hole mounting is typically reserved for bulkier components, such as electrolytic capacitors or semiconductors in large packages, that require additional mounting strength to withstand physical stress.
Hybrid technology
With the recent development, electronic products have become more and more complex. These complex electronic products require more complex, integrated and smaller size PCB boards.
It is almost impossible for a PCBA with only one component to perform such a complex task.
Therefore, for this purpose, a hybrid technology board with SMD and through-hole components will be required.
This type of board carries through-hole components and SMD components and requires a combination of through-hole technology and surface mount technology.
However, welding is a complex process that is often affected by too many elements. Therefore, better sequencing of through-hole technology and surface mount technology becomes very important.
The above briefly introduces several types of PCB assembly processes. If you want to customize PCB boards, please contact us.
Singo is a professional custom PCB board manufacturer, mainly engaged in PCB assembly and OEM/ODM electronic manufacturing services since 2006. Products involve medical equipment, home appliances, digital products, industrial control, etc. After years of hard work, we have established long-term cooperative relationships with some internationally renowned companies. If you are looking for electronic PCBA OEM/ODM supplier, welcome to contact us, we sincerely welcome you to visit our company.